Nex
Flush
The effects of being banned to home office during Corona...
I previously said I didn't see any reason to explore this area.
But now that I was repurposing all the spinners I got with my HCE CPC chips as a small separate set, my view has changed.
Making just three big racks in some nice colored material wouldn't be using that much filament that I'd have to buy additional spools, so I went for it. I still am unwilling to print so many racks that I could store one of my original CPC sets in whole in them (~3300/1600/1700 chips). Just for the tighter fit, it's definitely not worth it to me. For the looks though, the wood filament printed ones are awesome when stained.
My new Prusa Mini's build volume isn't big enough to spit out 5x20 racks, so I've been printing those on my MK3S. Instead, I made some 3x20s on the Mini.
These smaller racks are intended to be used by players at the table. Initially they would hold their starting stacks or standard buy-in, then once they are seated and placed their chips on the table, the rack could be used to put top-off/rebuy chips in them in a cash game to keep them separate from the live chips. (You buy these in advance, but they aren't live as long as they're in the rack. You can move chips from the rack to the table between hands to top off your live stack, and of course only up to the max allowed buy-in. Effect: less work with bank handling)
I built optimized custom support structures right into the models for the overhangs on the underside of the racks. Printing them is still tricky and requires the material to be used to have somewhat decent bridging performance, but you can break the supports away fairly easily with minimal residue, and they use much less material than autogenerated ones. The small wings on the underside of each barrel are there to keep a rack seated properly on top of another rack of chips.
Models are parametric, so I can generate them with any number of barrels and any barrel capacity. Barrel diameter adjustable as well of course. Even multiple rows of barrels are possible. Only limited by build volume of the 3D printer.
A 5x20 rack takes 7 1/2 hours to print and consumes about 80 grams.
The smaller 3x20 ones take 4 3/4 hours and 53 grams each.
This goes for a 0.4mm nozzle. Printing with a 0.6 obviously is faster, although they still take a lot of time (5 hours for 5x20).
Only took me two prototype prints until I ended up with a solid, working design. Even the prototypes worked, but on the first the chip fit was so tight that you'd have to pull out the barrels with force, and on the other, there was a rounding/detail error with the supports which led to some drooping filament on an otherwise successful print.
Had some failed 5x20 prints due to warping. The results also work, but don't look 100% good. Made some adjustments to placement on the print bed and now it works reliably in this aspect. A few more failed due to nozzle clogging from a filament spool that was tainted with foreign particles. New spool, fresh nozzle, all fine.

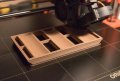
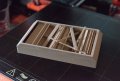
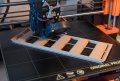
I previously said I didn't see any reason to explore this area.
But now that I was repurposing all the spinners I got with my HCE CPC chips as a small separate set, my view has changed.
Making just three big racks in some nice colored material wouldn't be using that much filament that I'd have to buy additional spools, so I went for it. I still am unwilling to print so many racks that I could store one of my original CPC sets in whole in them (~3300/1600/1700 chips). Just for the tighter fit, it's definitely not worth it to me. For the looks though, the wood filament printed ones are awesome when stained.
My new Prusa Mini's build volume isn't big enough to spit out 5x20 racks, so I've been printing those on my MK3S. Instead, I made some 3x20s on the Mini.
These smaller racks are intended to be used by players at the table. Initially they would hold their starting stacks or standard buy-in, then once they are seated and placed their chips on the table, the rack could be used to put top-off/rebuy chips in them in a cash game to keep them separate from the live chips. (You buy these in advance, but they aren't live as long as they're in the rack. You can move chips from the rack to the table between hands to top off your live stack, and of course only up to the max allowed buy-in. Effect: less work with bank handling)
I built optimized custom support structures right into the models for the overhangs on the underside of the racks. Printing them is still tricky and requires the material to be used to have somewhat decent bridging performance, but you can break the supports away fairly easily with minimal residue, and they use much less material than autogenerated ones. The small wings on the underside of each barrel are there to keep a rack seated properly on top of another rack of chips.
Models are parametric, so I can generate them with any number of barrels and any barrel capacity. Barrel diameter adjustable as well of course. Even multiple rows of barrels are possible. Only limited by build volume of the 3D printer.
A 5x20 rack takes 7 1/2 hours to print and consumes about 80 grams.
The smaller 3x20 ones take 4 3/4 hours and 53 grams each.
This goes for a 0.4mm nozzle. Printing with a 0.6 obviously is faster, although they still take a lot of time (5 hours for 5x20).
Only took me two prototype prints until I ended up with a solid, working design. Even the prototypes worked, but on the first the chip fit was so tight that you'd have to pull out the barrels with force, and on the other, there was a rounding/detail error with the supports which led to some drooping filament on an otherwise successful print.
Had some failed 5x20 prints due to warping. The results also work, but don't look 100% good. Made some adjustments to placement on the print bed and now it works reliably in this aspect. A few more failed due to nozzle clogging from a filament spool that was tainted with foreign particles. New spool, fresh nozzle, all fine.

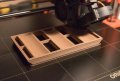
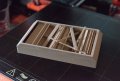
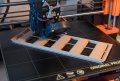