Note: The first few portions of this thread are copied from PMC. The Workbench is an ongoing work in progress and will be updated periodically.
About two months ago, I got a wild hair up my ass to take up woodworking as a hobby. The first project I decided to undertake was to build a legitamate workbench. My thought on this was that it would be a useful tool for many years regardless of if I actually follow through and continue to do woodworking projects or not and at a minimum it would teach me a shit load of new skills. After much research on youtube, I decided to use Jay Bates workbench as a guide for the one I wanted to build. A relatively simple design (much less involved and less expensive compared to a roubo style bench) but solid as all hell and perfect for all sorts of projects in the future.
The first dilemma to tackle was that I was severely limited in two ways - money and space. Money was a big factor because I just don't have many tools yet, and space was another consideration since many shop tools are huge. My work area is half of a small 2-car garage and ideally I'd like to park the car in the garage when I'm not actively working on projects. The first stop was raiding my dad for some old tools that he acquired many years ago and probably hasn't used in 30-40 years. The three tools I "borrowed" are a Stanley No. 5 Jack Plane, a draw knife, and a combination square. The draw knife (probably won't be used for the workbench project) is just rusty and needs a sharpening and the square is rusty and the rule is slightly bent, but the big job here is restoring the jack plane. Here's a few pics of how these looked when I took possession of them.
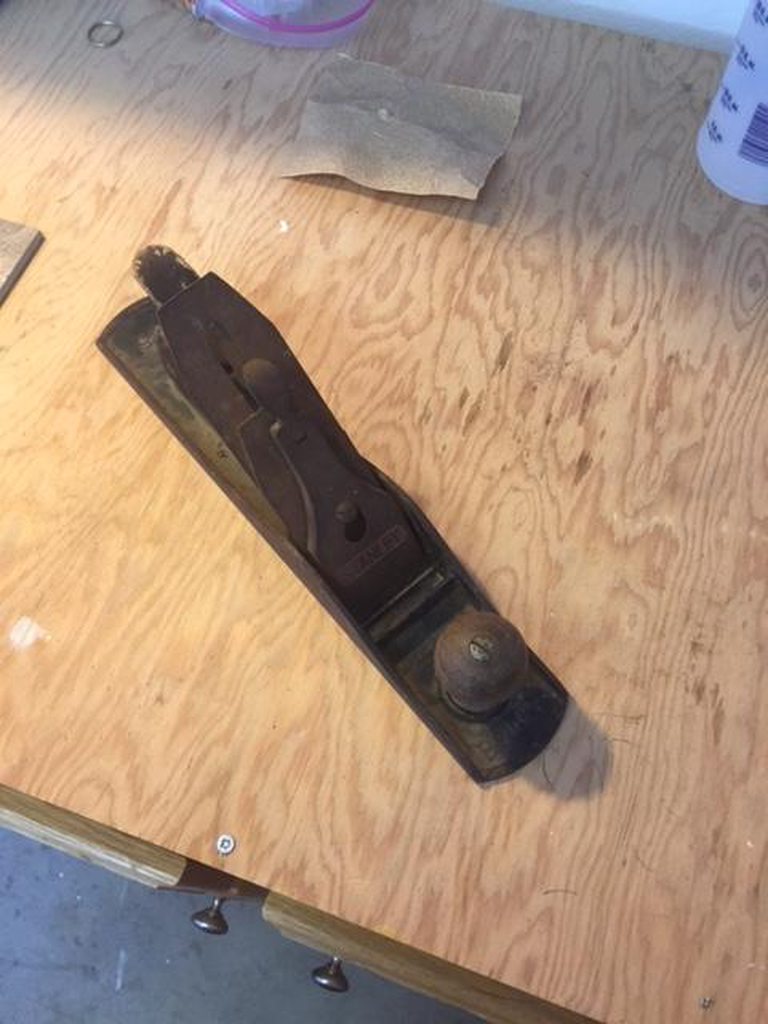
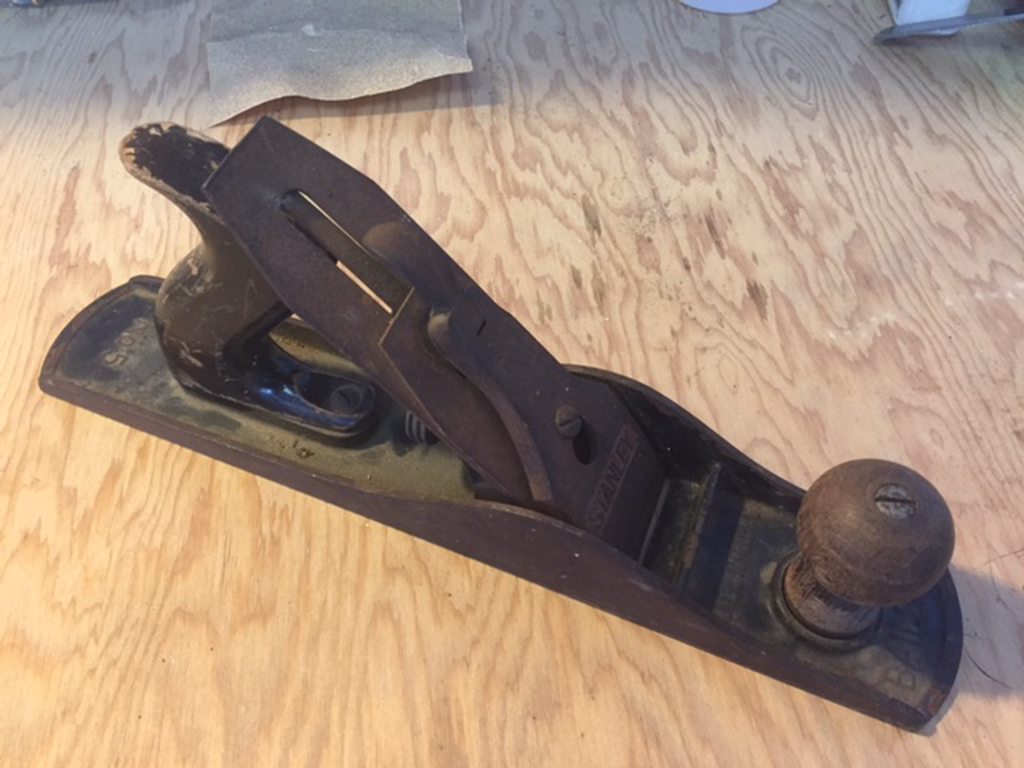
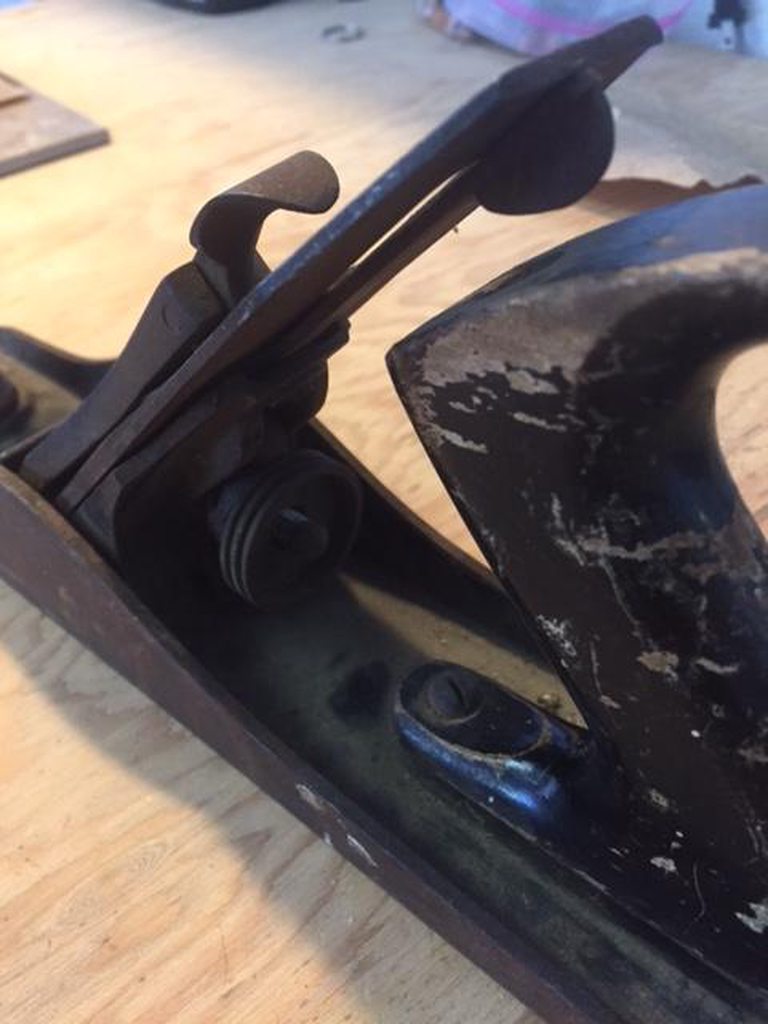

First I got the rusty parts of the draw knife and square soaking in diluted white vinegar to help remove the rust, then I turned my attention to the plane. First step there was to remove the rust and flatten the sole using a relatively coarse sand paper. It's worth noting that counter intuitively you should flatten the sole fully assembled. When the blade and frog are clamped down it will slightly change the flex of the shoe. If you disassemble and then flatten the sole, the shoe will warp when you reassemble and then you'd have to redo the work to reflatten the sole.
Getting started...

After about 5 minutes of work...
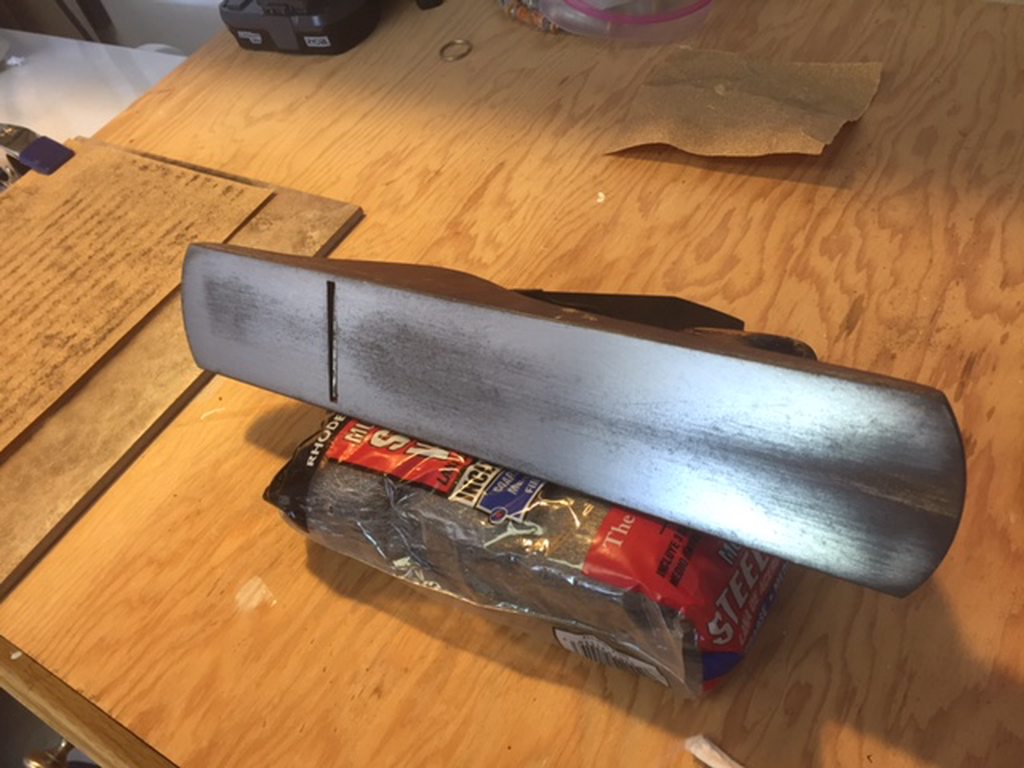
Another 5 minutes...

You can see where the high spots on the sole are based on where the rust/discoloration remains and where the sand paper has progressively flattened down to reveal bare steel. Once I got the sole pretty well flattened out I started work on the sides as well. These are some finished shots of the sole and the sides.
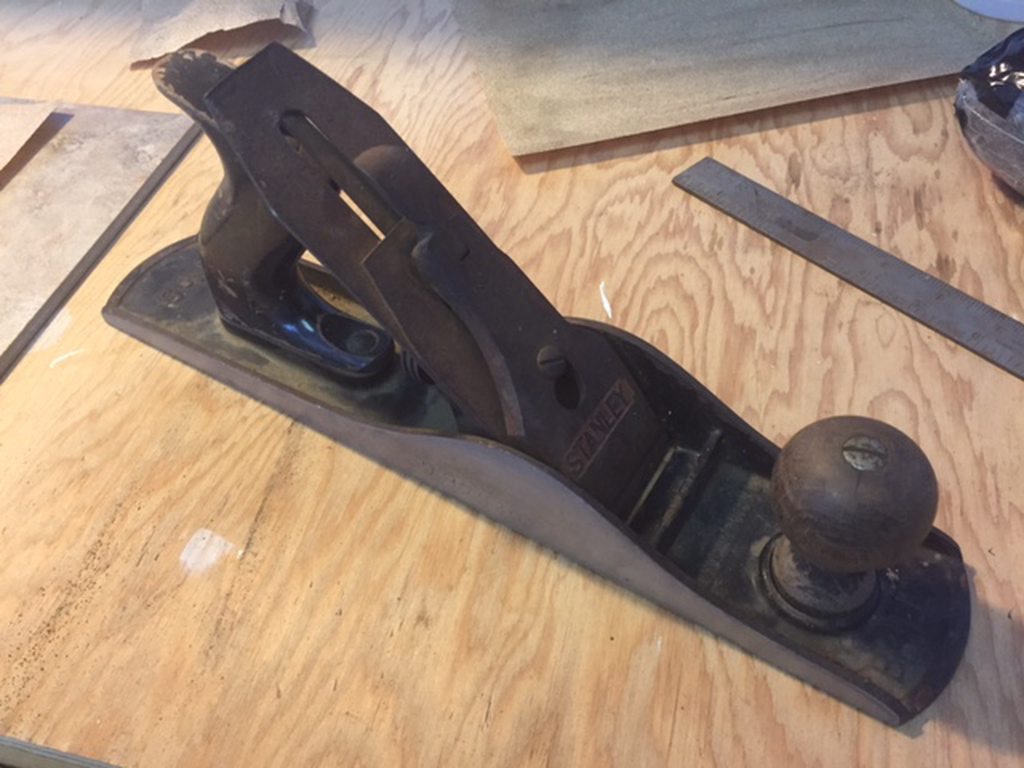
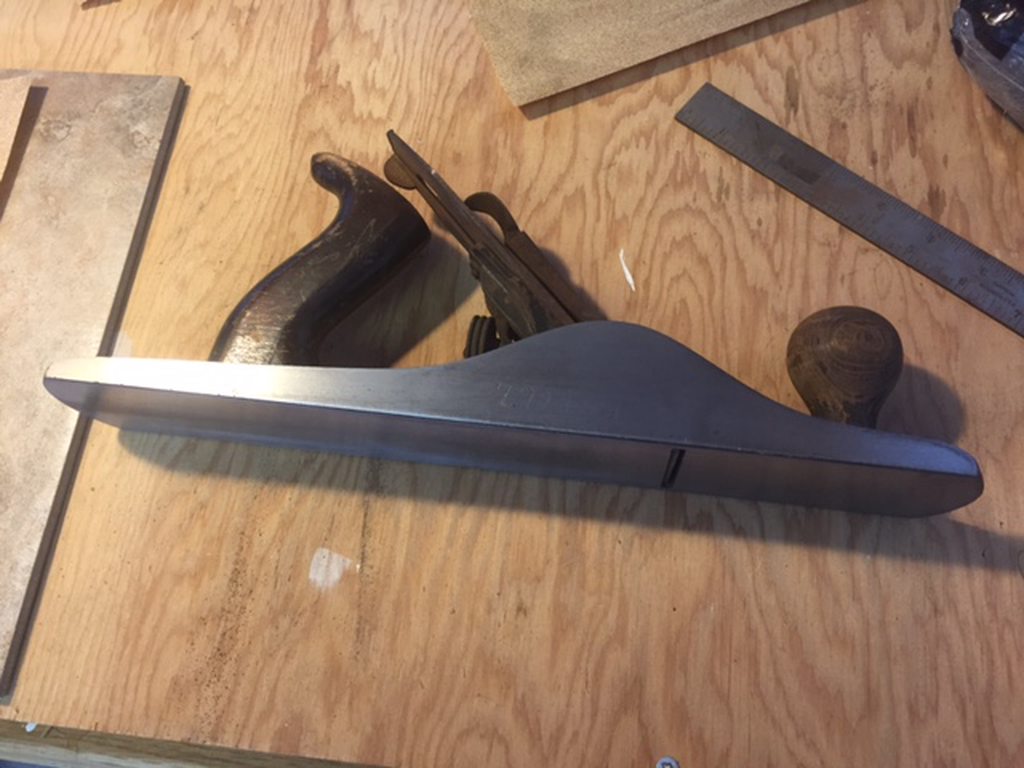
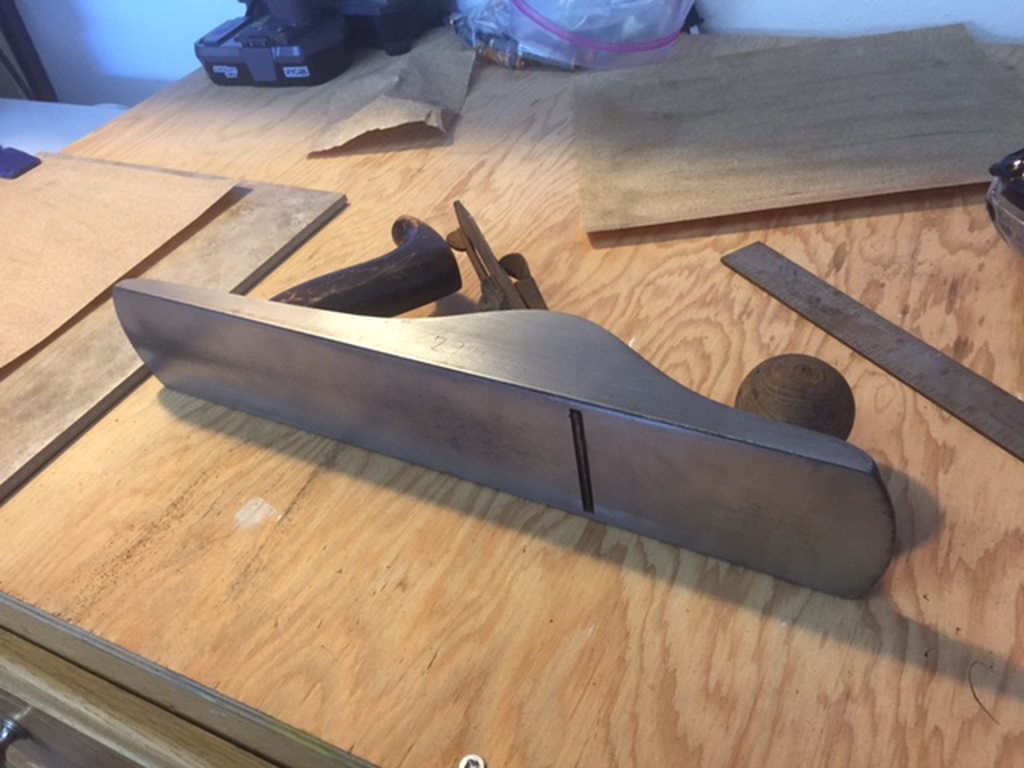
By now the other tools were ready for some attention. I disassembled the plane and got all the rusted parts (other than the shoe) into the vinegar for a soak.


In the meantime I used a wire brush and some steel wool on the draw knife and square to remove the rust and finished the square with some 3 in 1 oil. The draw knife needs more work and then sharpening so that will come later.
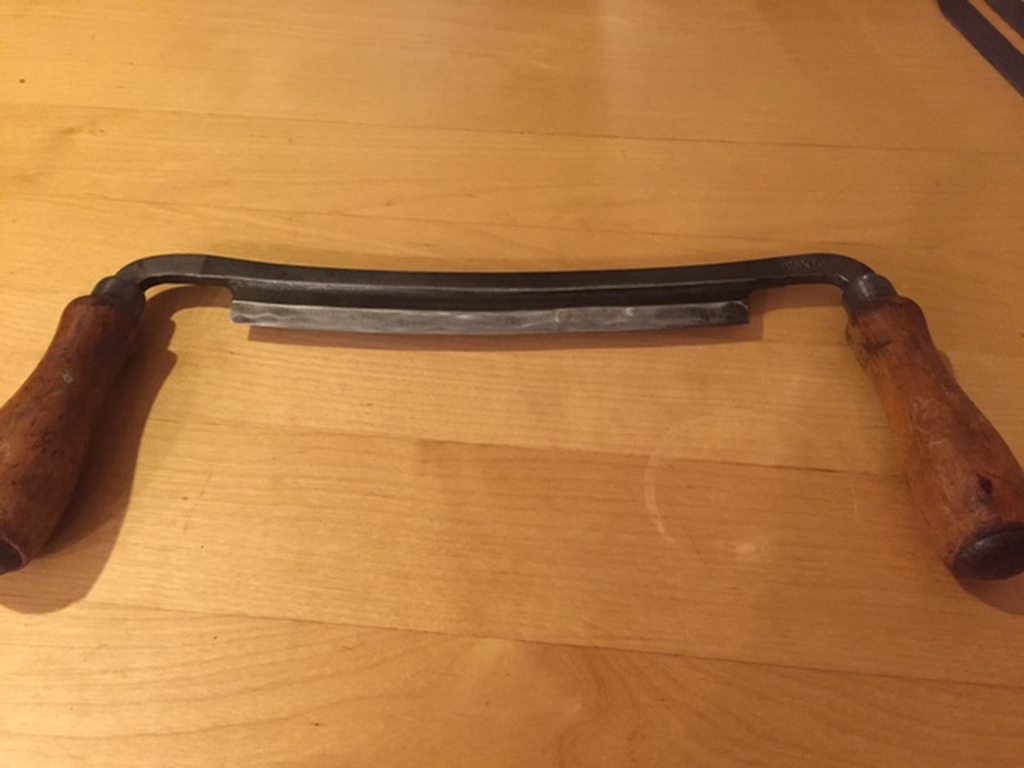
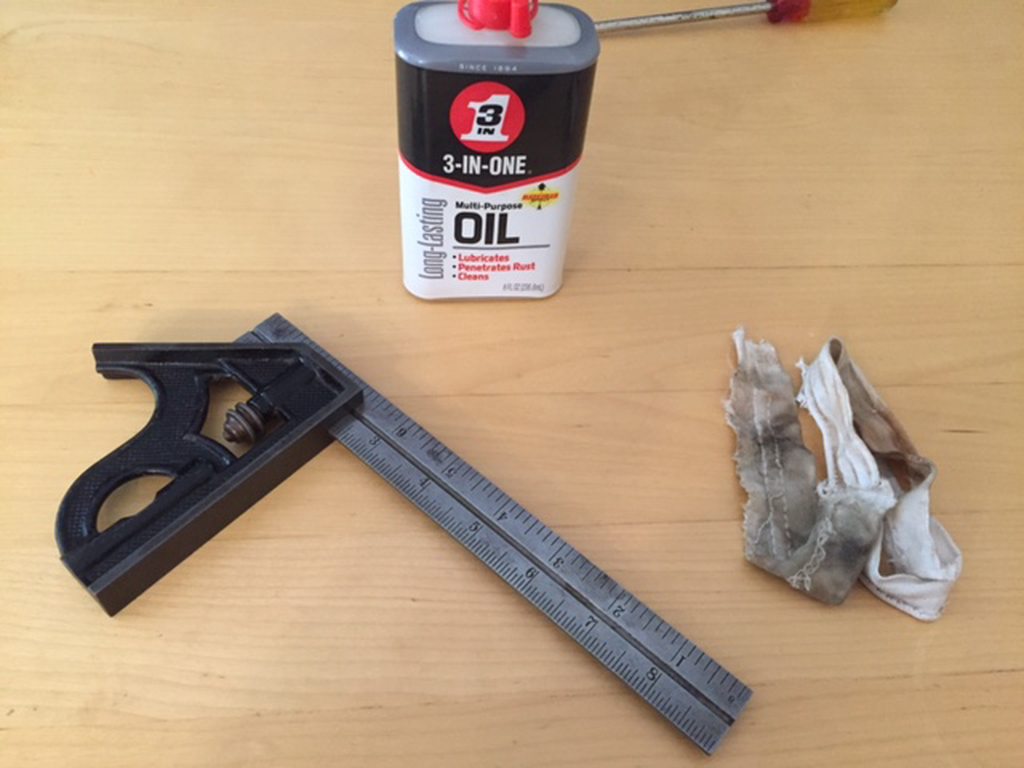

About two months ago, I got a wild hair up my ass to take up woodworking as a hobby. The first project I decided to undertake was to build a legitamate workbench. My thought on this was that it would be a useful tool for many years regardless of if I actually follow through and continue to do woodworking projects or not and at a minimum it would teach me a shit load of new skills. After much research on youtube, I decided to use Jay Bates workbench as a guide for the one I wanted to build. A relatively simple design (much less involved and less expensive compared to a roubo style bench) but solid as all hell and perfect for all sorts of projects in the future.
The first dilemma to tackle was that I was severely limited in two ways - money and space. Money was a big factor because I just don't have many tools yet, and space was another consideration since many shop tools are huge. My work area is half of a small 2-car garage and ideally I'd like to park the car in the garage when I'm not actively working on projects. The first stop was raiding my dad for some old tools that he acquired many years ago and probably hasn't used in 30-40 years. The three tools I "borrowed" are a Stanley No. 5 Jack Plane, a draw knife, and a combination square. The draw knife (probably won't be used for the workbench project) is just rusty and needs a sharpening and the square is rusty and the rule is slightly bent, but the big job here is restoring the jack plane. Here's a few pics of how these looked when I took possession of them.
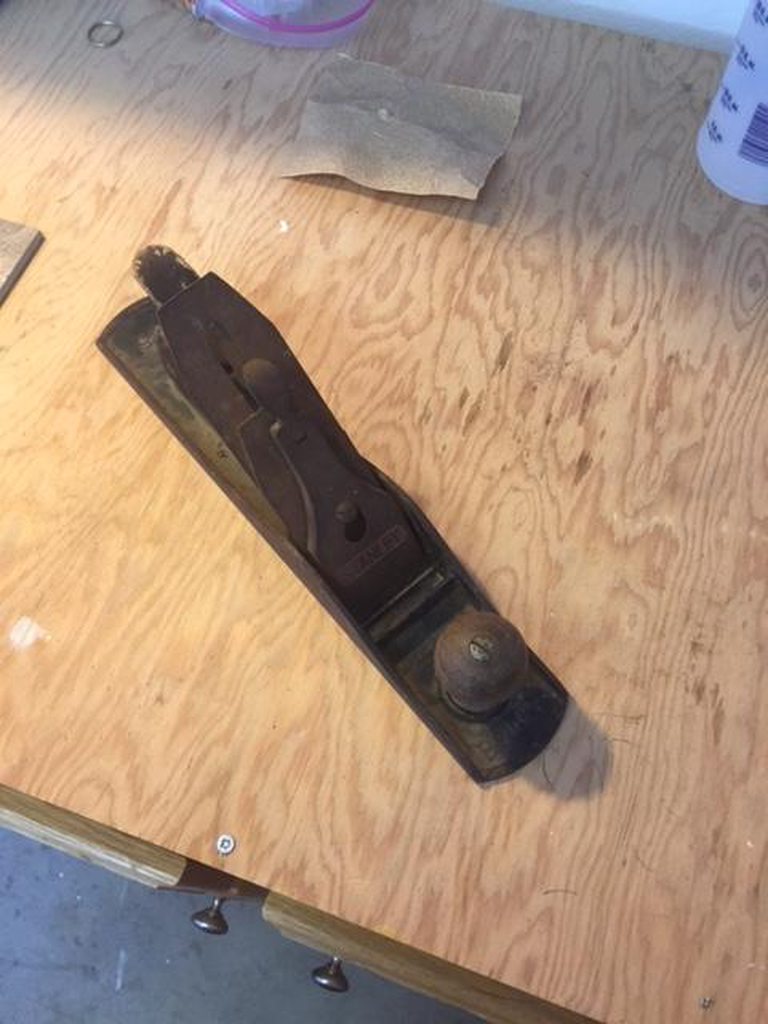
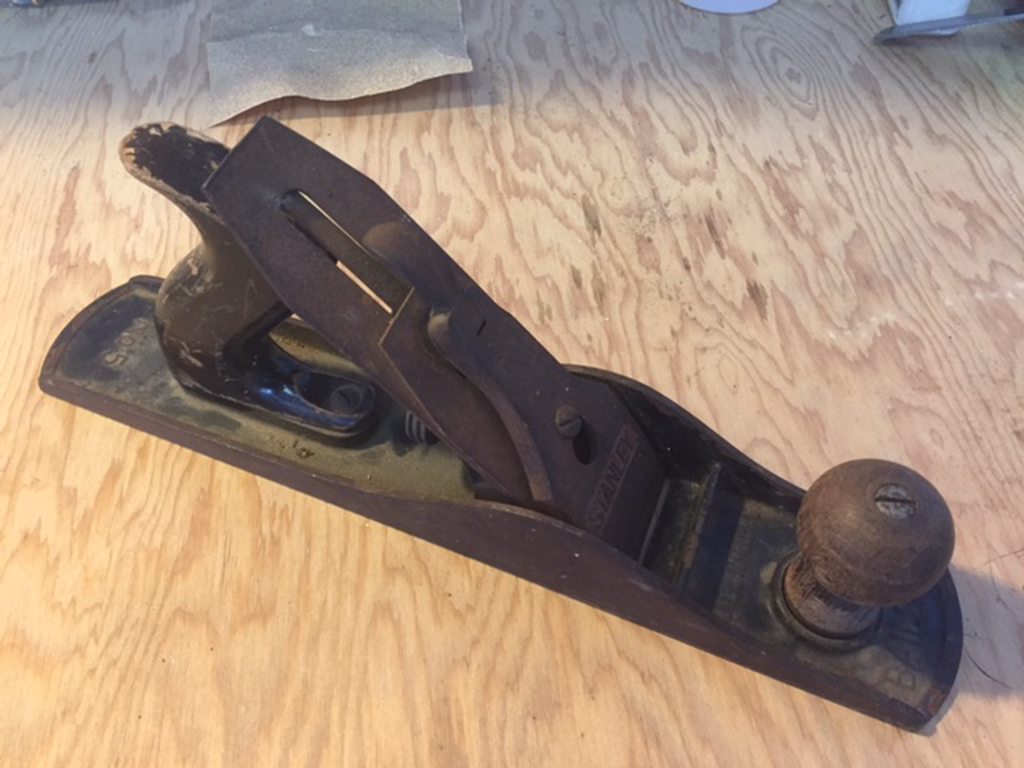
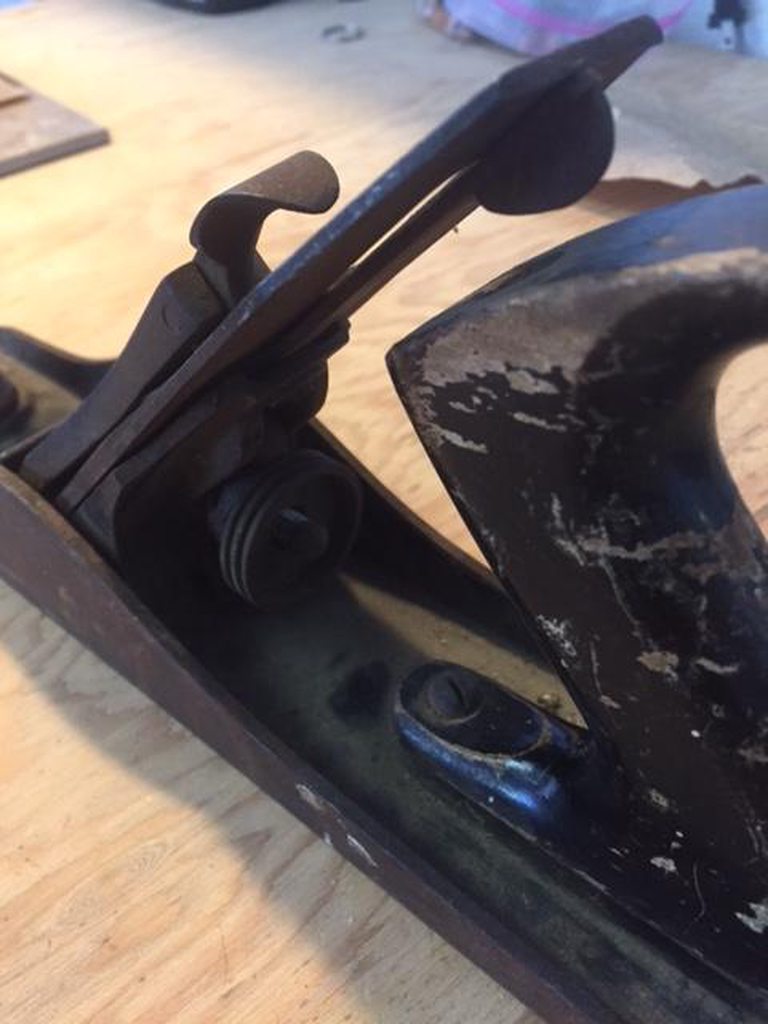

First I got the rusty parts of the draw knife and square soaking in diluted white vinegar to help remove the rust, then I turned my attention to the plane. First step there was to remove the rust and flatten the sole using a relatively coarse sand paper. It's worth noting that counter intuitively you should flatten the sole fully assembled. When the blade and frog are clamped down it will slightly change the flex of the shoe. If you disassemble and then flatten the sole, the shoe will warp when you reassemble and then you'd have to redo the work to reflatten the sole.
Getting started...

After about 5 minutes of work...
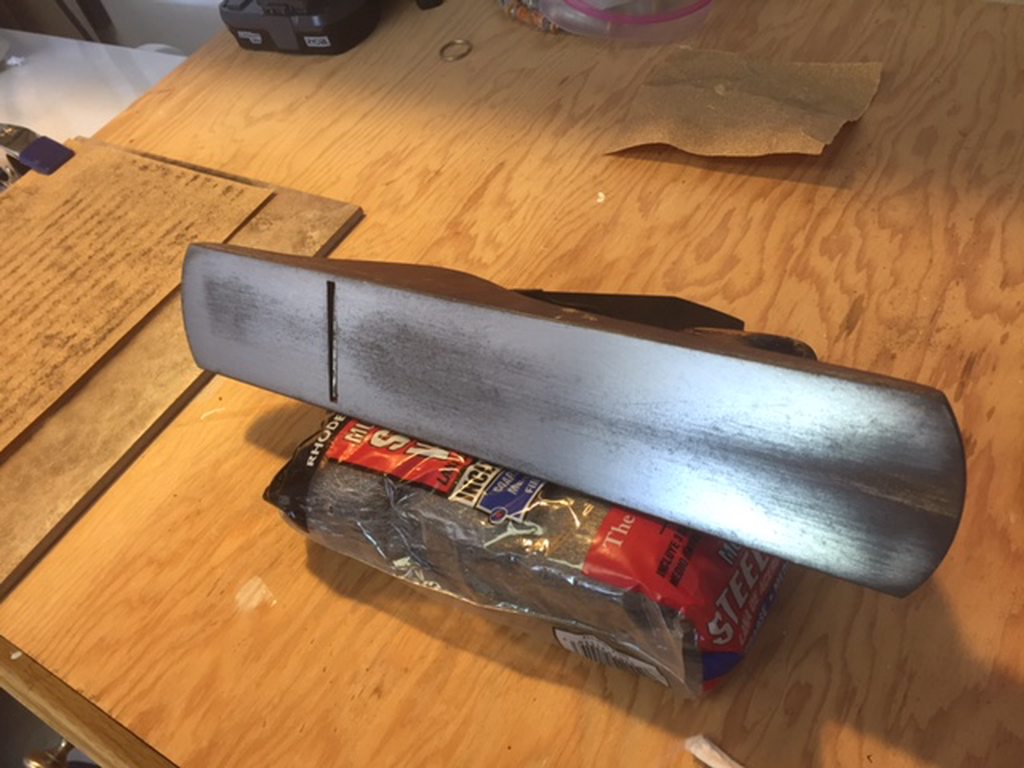
Another 5 minutes...

You can see where the high spots on the sole are based on where the rust/discoloration remains and where the sand paper has progressively flattened down to reveal bare steel. Once I got the sole pretty well flattened out I started work on the sides as well. These are some finished shots of the sole and the sides.
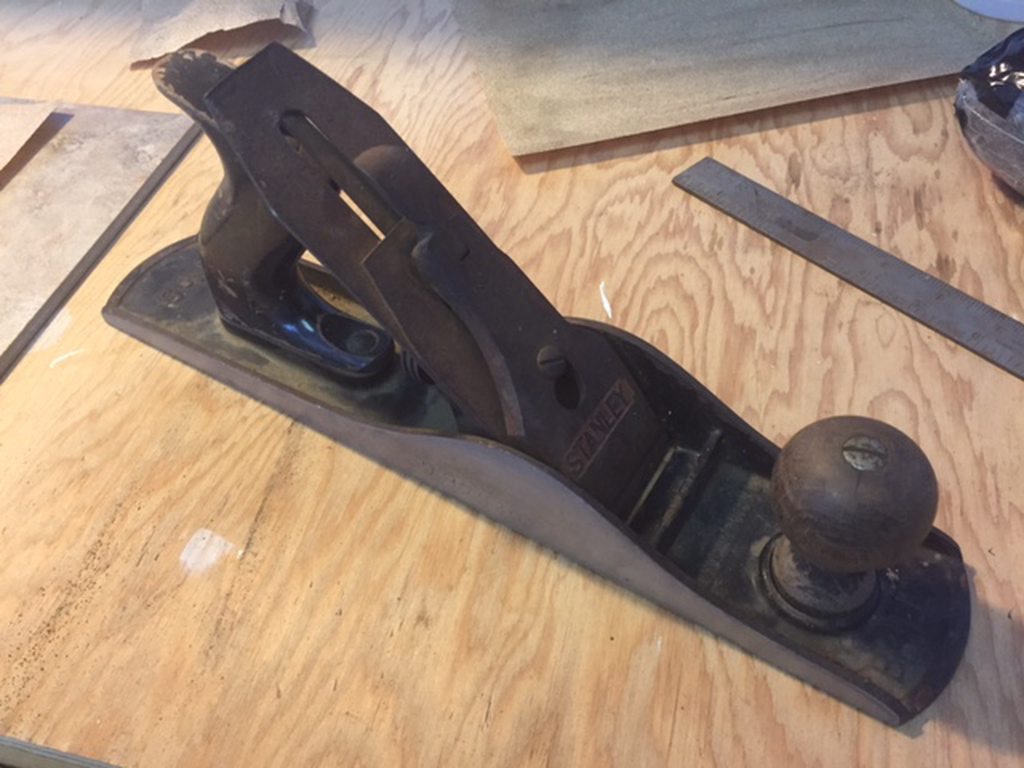
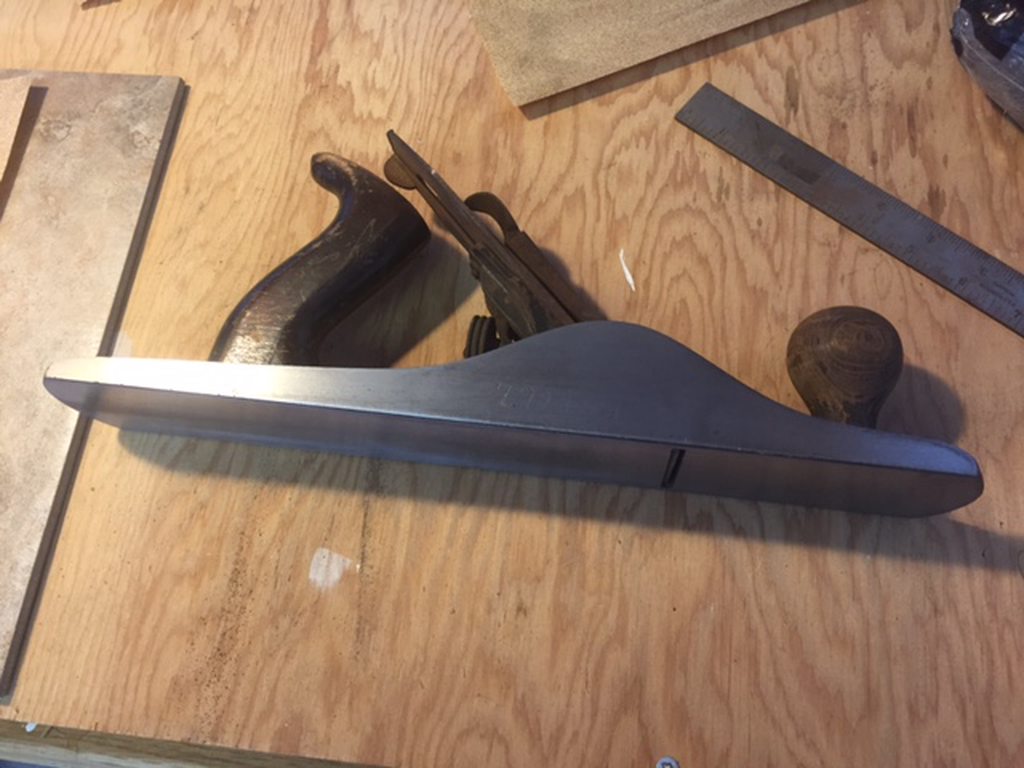
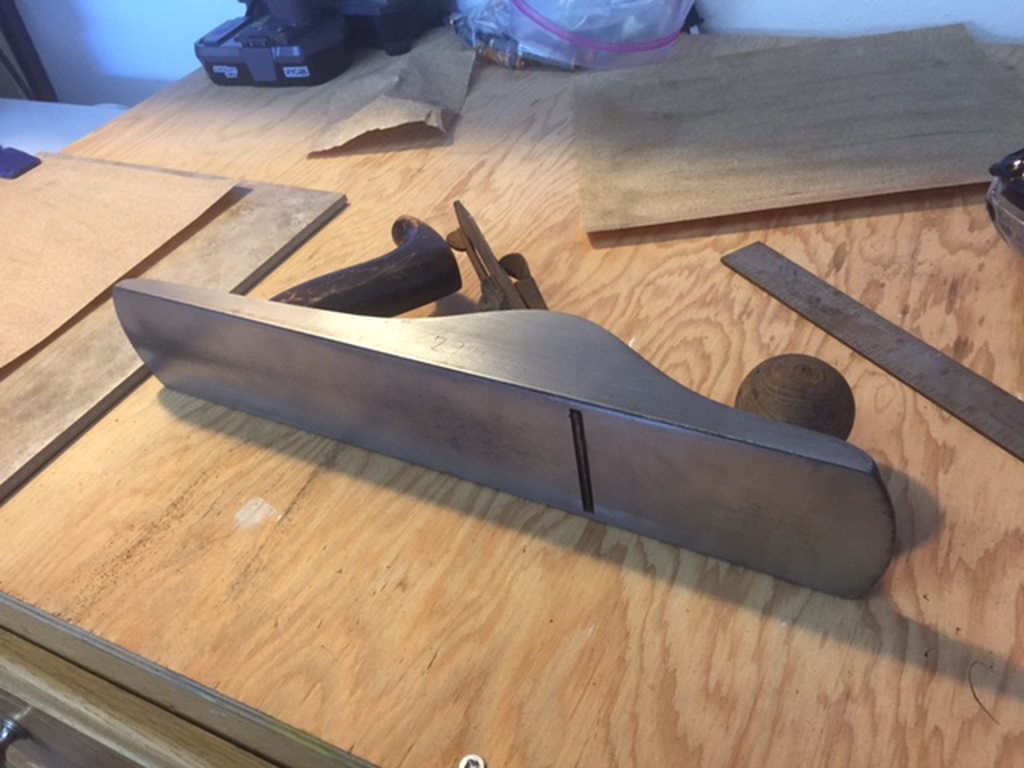
By now the other tools were ready for some attention. I disassembled the plane and got all the rusted parts (other than the shoe) into the vinegar for a soak.


In the meantime I used a wire brush and some steel wool on the draw knife and square to remove the rust and finished the square with some 3 in 1 oil. The draw knife needs more work and then sharpening so that will come later.
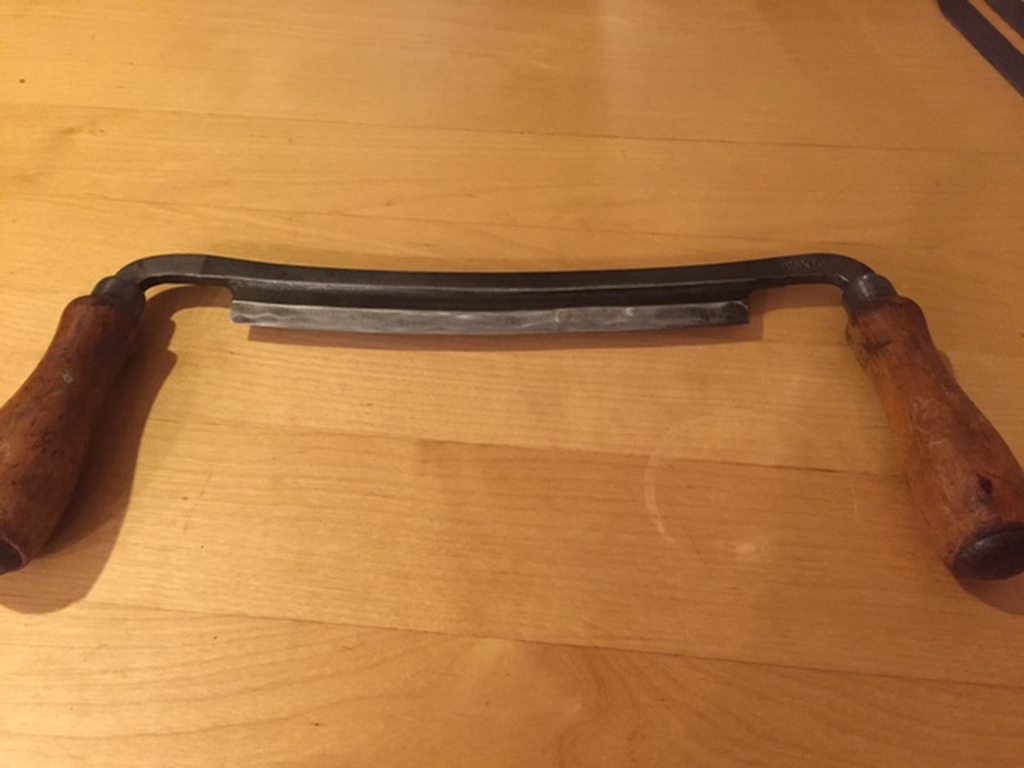
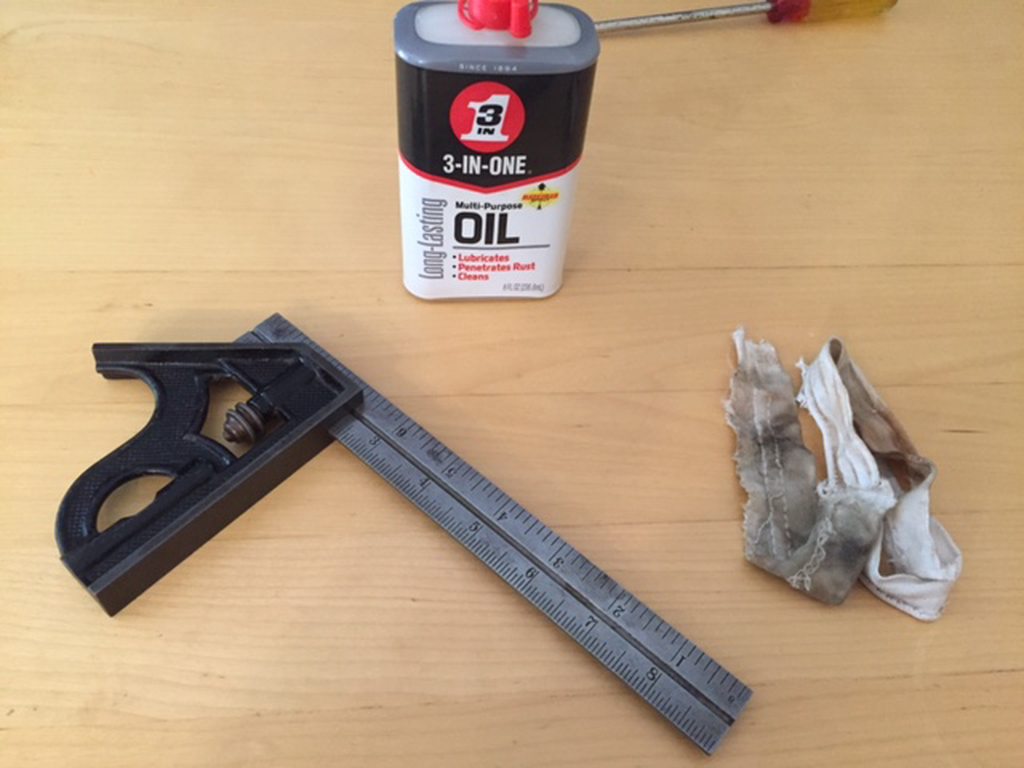
